
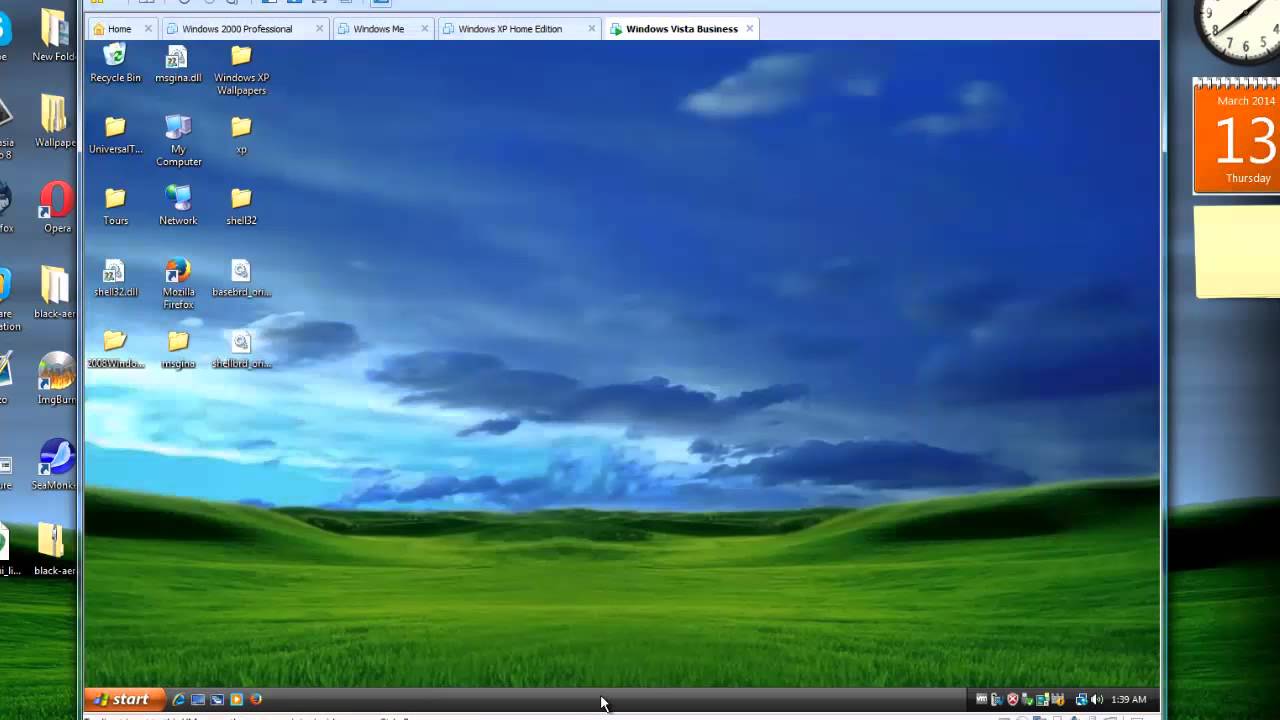
Exact calculations of the fluid–structure interaction and the pressures and impulses transferred to the structure require sophisticated coupled Euler–Lagrangian computations.
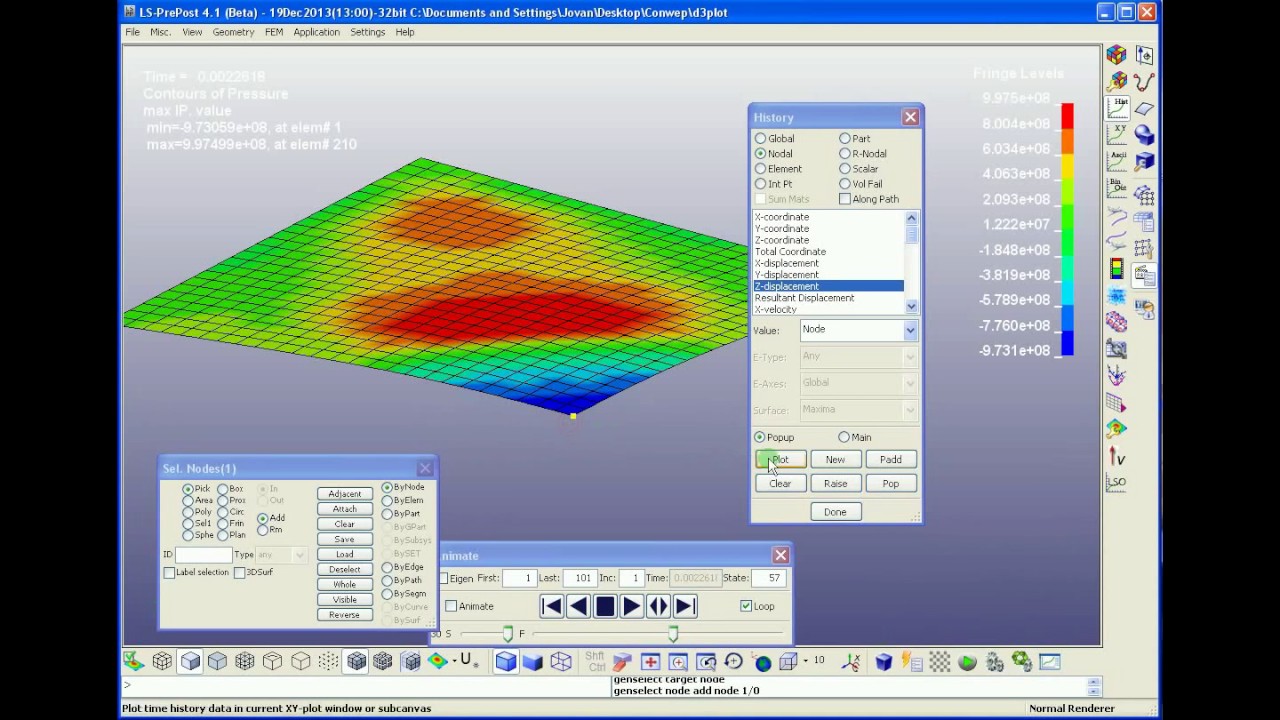
However, values up to 20 have been reported when real gas effects such as the dissociation and ionization of air molecules are considered. For strong shocks in ideal gases, the theoretical limit for the reflection coefficient is 8. However, the magnification can be highly non-linear and depends upon the degree of compression of the incident shock and the constitutive response of air. For weak shocks in air, the reflection is linear and the reflection coefficient is 2.
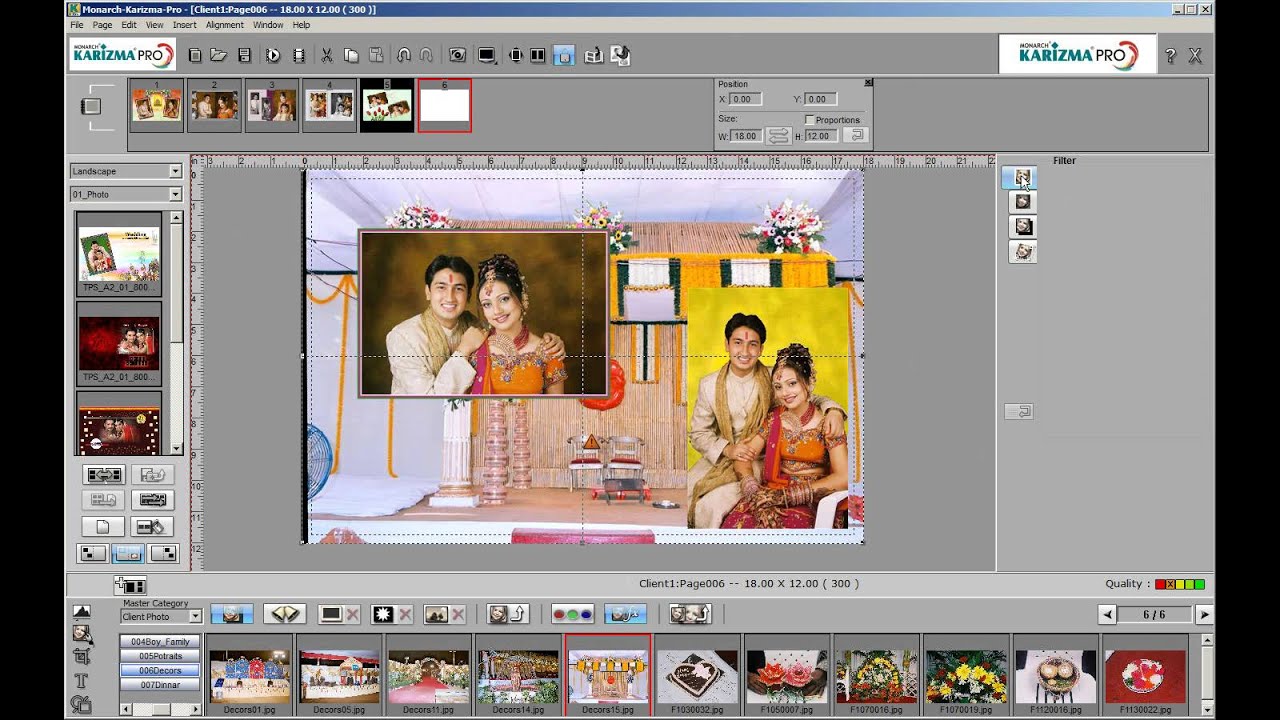
When the (compressed) shock encounters a surface, it is reflected, amplifying the overpressure. In this simplified description, the wave propagates to the right within the domain x 0 without changing its shape and reaches the plate at time, t 1⁄4 0. p ( x, t ) is the pressure at a point x and time t, p o is the maximum incident overpressure, t i is the wave decay time and a 0 is the sound speed in air. This calculation affirms that problems arise if the foam thickness is insufficient and ascertains the magnitude of the transmitted overstress when this happens. At h 1⁄4 h min 1⁄4 10 cm, the foam completely crushes after about 3.4 ms and large stress oscillations develop when the moving buffer pushes into the crushed foam. It remains to be determined whether these oscillations are transmitted and could cause injury. However, there are superimposed oscillations, which attain stresses as high as 0.4 MPa, albeit for short times. Moreover, the buffer arrests before the foam attains its densification strain. 6) reveal that, at h 1⁄4 15 cm, the foam crushes with average transmitted stress remaining below the threshold pressure. The simulations have been performed using a foam thickness h 1⁄4 10 and 15 cm. (1), with t i z 0 : 044 ms and p 0 z 2 : 5 MPa, such that the impulse I total z 1 : 1 kPa s. The foam is considered to be rate insensitive (typical for Al alloys) and the impulse is imparted to the buffer as a pres- sure/time history of the type expressed by Eq. The calculations have been conducted using ABAQUS/Explicit. To substantiate these analytic results, decoupled dynamic simulations of crushing have been performed using the same foam and various buffer plates. More intense impulses require yet more bulky systems. 2), by using a buffer with a mass of 20 kg/m 2, a minimum foam thickness, h min 1⁄4 10 cm is required. Note that to mitigate a 1 kPa s impulse, corresponding to a 3 m standoff (Fig. 2, the minimum foam thickness has been calculated as a function of stand-off distance for buffers with a mass per area of 8, 20 and 40 kg/m 2 (corresponding to 1, 2.5 and 5 mm of steel, respec- tively) as plotted in Fig. The preceding formulae are used to construct mitigation curves for a fixed explosive mass (10 kg of TNT) using an Al alloy foam with 5% relative density that compresses at 0.28 MPa (just below the injury threshold of 0.3 MPa).

s pl 1⁄4 p th is specified as the constraint, then for a given impulse, the density terms are the only parameters affecting the minimum mass.
